Working Model 2D
2D Dynamic Motion Simulation
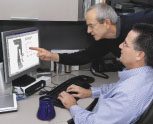
Electrical OEM Puts Motion Analysis Software to the Test
According to Sergei Fedorjaczenko, a design engineer at Carlingswitch, circuit breaker analysis is similar to conducting an autopsy; much of the data is destroyed during the triggering of the switch. Working Model allowed Fedorjaczenko to simulate the motion of a circuit breaker and collect all the data he needed -- streamlining new product testing.
Carlingswitch of Plainville, Connecticut
is an original equipment manufacturer of magnetic circuit breakers and
electrical switches for the appliance, transportation, and HVAC industries.
One of the more tedious, time-consuming tasks of switch and breaker design
is making prototypes for testing the responses of new designs. This "build
and try" method can take months just to make and assemble the prototype
parts before a test is run, a test that is only milliseconds in duration.
In that short span of time, the prototype is often deliberately destroyed
through bursts of high current, and then the painstaking work of analyzing
the failure begins. At this stage, the designer would be in for many more
weeks of refining and testing, until a new method of testing was discovered.
Carlingswitch experimented with this new testing method, often called "virtual prototyping," which utilizes motion analysis software from Design Simulation Technologies. Working Model® allows engineers to test a mechanism on a desktop computer and know with a high degree of accuracy whether it is feasible to build and whether the device will perform as intended. Carlingswitch runs Working Model on the Macintosh, but an equally powerful Microsoft® Windows version is also available.
Testing Speed & Power
Carlingswitch circuit breakers are analyzed for two types of
response: speed and power, measuring how fast contacts open to prevent
a surge of damaging current. The circuit breaker's response time has to
be measured either by onboard instrumentation or by high-speed photography.
A power test involves measuring current to determine if a breaker will withstand interruptions. If not, the sparks and the parts fly. Only through these testing methods were Carlingswitch personnel able to see a prototype circuit breaker's effectiveness.
The problem with these previous testing methods is that arcing can hamper the photographic method of analysis by causing a white-out effect that makes photographic results difficult to interpret, while fried prototype components make instrumenting just as difficult to tell the sequence of a destructive event (determining which springs and contacts failed when).
What makes the analysis even more difficult is that Carlingswitch circuit breakers are not big: the smallest ones are approximately 1-1/2" square and 1/2" thick; the largest are 3" x 5" x 1" thick. Instrumenting and photographing such small prototypes is not an easy task.
Given these testing and analysis problems, design engineer Sergei Fedorjaczenko decided to put Working Model to the test to determine whether virtual prototyping could save Carlingswitch money and improve the company's design-to-market time.
Fedorjaczenko said, "I've been building models of some of our existing products, running simulations and comparing the results with data we have on the actual performance of these products. This allows me to develop a confidence factor in the Working Model simulation engine and to fine tune the simulation so that it represents what actually happened with a particular mechanism. With that confidence factor, I can work with a new design, begin changing geometry and properties like weights of parts and so forth, try different spring forces, and then use the simulator to predict how performance will be affected."
"Excellent GUI."
Developing a simulation in Working Model was a logical, straightforward
process. Fedorjaczenko imported one circuit breaker design from his Ashlar
Vellum CAD system using DXF file formats. He then assembled the circuit
breaker's various components in their proper relationship to each other.
The Working Model menu let Fedorjaczenko insert joints, stops, and spring
forces in the proper locations.
"I've used other simulators before," explained Fedorjaczenko, "but the thing I like most about Working Model is that it has an excellent graphical user interface [GUI]. The geometry of a simulation is easy to create within Working Model, but it's just as easy to import my own geometry. And you don't have to prepare any kind of input file. I generally try and simplify geometry wherever possible so I don't bring in a great deal of unnecessary data. I don't have to show intricate details on the parts, as long as the part functions as it should and is represented with the proper mass and inertia.
"What Working Model does is break down the simulation into finite steps, performing a series of calculations at each time-step or interval. That is one reason you don't want to overburden your mechanism with too much detail. The more things the simulator has to check at each time-step, the longer the simulation will take."
Once the model is built, it's easy to update and change variables, such as the mass of an object, or the force applied to a rod or actuator. Working Model will automatically assign values of mass and friction to objects in the simulator, or modify those variables easily because the GUI is simple to use. For example, Fedorjaczenko used Working Model to develop an equation of his own that let him simulate the magnetic force or pull exerted by a solenoid on a circuit breaker armature.
"I took data from a previous test we had done, because I knew how fast this armature responded to the pull of the solenoid. The equation was then adjusted until the simulated armature responded as it did in real life. Once this equation was developed, I was able to run a simulation and determine what the responses would be when the current was altered."
Working Model's powerful simulation engine allowed Fedorjaczenko to confirm his suspicions about the responses of this particular circuit breaker: "It verified that we were getting abrupt, sharp impacts with the contact -- something we thought might be happening but really had no way to instrument or verify precisely using any other method."
Checking the Data.
Fedorjaczenko likens examining a destroyed circuit breaker prototype
to an autopsy, noting, "In the event of a failure, we try to see
what failed first and why. These events usually involve an interruption
of current, which means an event lasting no longer than 10 to 20 milliseconds.
Very often, the conclusions of this autopsy are speculative and not very
precise. You get a feel for it, but you're still not quite sure."
Fedorjaczenko used Working Model's on-screen graphic simulation to check that the simulation was running correctly. The tables and other data output provided by the simulation itself let him evaluate what needed to be changed in order to improve the results. Working Model can write to external files, including data files or to Microsoft Excel.
"A lot of the analysis portion of prototype testing takes place after the simulation, when you sit and look at a velocity curve or some other piece of data and decide what's required next, and Working Model easily generates that kind of output," said Fedorjaczenko. "It only takes about five or ten minutes to change a variable and run a particular simulation again, so you're able to do a lot of 'what ifs'. I went through literally dozens of these 'what ifs' in a matter of hours."
Now that he's tested Working Model 2.0, Fedorjaczenko believes in the product and its capabilities as a way to streamline the testing phase of new products. By reducing the number of destructive tests necessary to study a new circuit breaker design, Carlingswitch will save countless worker hours and modeling materials, a significant savings when factored over the course of just a few months. The motion analysis provided by Working Model is highly accurate, so Fedorjaczenko will be able to rely on the results of future simulations with confidence. Fedorjaczenko confirms, "I think Working Model is a great tool. In just three months I've already verified for myself and my management that this is a tool we should all be using on a regular basis in the design of our new products."