Working Model 2D
2D Dynamic Motion Simulation
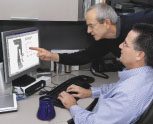
Engineering Cams in the Virtual World
Abbott Labs sidesteps trial and error re-engineering with simulation software from Design Simulation Technologies
While virtual prototyping is popularly regarded as the ticket to more efficient product and design development, many engineers today use the process to optimize the performance of existing products and equipment.
Through the use of Working Model motion analysis software from Design Simulation Technologies, Abbott Labs is realizing the promise of re-design through virtual prototyping; making assembly line machinery faster, more reliable and operator friendly without the expense of building a physical model or testbed.
"Creating a simulation allowed us to identify the problem in our equipment, install a replacement part and have the whole thing functioning perfectly the first time," says Randy Fergen, an Engineer in Abbott Labs' Diagnostics Division.
Abbott Labs is no stranger to innovation. The health care giant is a leader in the development of nutritional, pharmaceutical, diagnostic, and hospital equipment and distributes products from production centers around the world. But before Abbott adopted a simulation software solution, design problems at such facilities, whether for new equipment or a retrofit, were rarely solved so quickly or easily.
"When troubleshooting a critical area on an existing piece of equipment, we sometimes had to make adjustments or modifications until the machine was performing reliably in the robust manner which manufacturing equipment demands," says Fergen. "In the past, re-design meant a couple weeks crunching numbers and designing parts, submitting the drawing for fabrication, then waiting weeks more for the machine shop to turn the project around."
To improve engineering and design practices Fergen and his associates began searching for a simulation system that would eliminate time and materials waste without incurring high purchase or maintenance costs. Design Simulation Technologies's Working Model addressed that need perfectly.
Nailing Down the Problem
Recently, Fergen put Working Model to the test in the redesign of a pick-and-place machine used for assembly of diagnostic products. Excessive vibration in the machine was responsible for unusually high noise levels, restricted machine speed, and abnormally frequent service. As the problem persisted, the company experienced diminished throughput.
Careful observation by Fergen and his team suggested that the vibration was attributable to a cam operating in the pick-and-place function. The profile of the cam resulted in a rigid and jarring pattern of motion in which the substantial and rapidly accelerating mass of the placement mechanism would come to a violent halt before making each of the four 90 degree motions in its cycle.
Fergen deduced that a smoother cam profile with fewer dwells would result in a more fluid motion; reducing vibration, noise, and the wear associated with a cycle of high impact mechanical movements. Aware that the previous cam would be replaced, Fergen elected to conduct the redesign in Working Model. He hoped that simulations on screen would reveal precisely which deficiency in the cam profile was responsible for the vibration and which modifications would result in more effective operation.
Fergen's initial observations of the machine itself revealed just how challenging the redesign would be. "It was obvious that the original manufacturer didn’t fully consider the acceleration profile and inertia that this cam would generate at higher speeds," according to Fergen. "The original cam design was very generic without regard to harmonic motion, masses or velocities that would potentially be involved in this pick-and-place application."
Matters were further complicated by the absence of a timing diagram to illustrate ideal performance parameters for the cam. "The motion involved was very generally defined," says Fergen. "The timing diagram we had on hand used straight diagonal lines to define the motion profile rather than a sin wave or curvilinear measurement. We were still searching for a method to illustrate the symptoms we had observed."
From Raw Data to Real Time
Determining problematic aspects of the cam's properties for graphic analysis required strict definition of the cam's existing motion profile. For this process at least, old-world engineering techniques came in handy: Fergen took caliper measurements of all critical interactive motion activities at every encoder increment of the machine’s cycle and converted the data to distance displaced per degree of motion.
From that point on, Fergen's analysis took place in the electronic domain. Caliper readings were placed in a Excel spreadsheet to create a referenceable timing diagram of the machine’s motion. Next, Fergen designed individual components of the machine in 2D with AutoCAD to be transferred as DXF files to Working Model.
Once separate components were reassembled in Working Model, Fergen imported data from the Excel timing diagrams through a DDE link to drive the animation. "The look-up table from Excel became a program telling the components exactly how to run," Fergen states. "We were working with very exact data that we had compiled and verified so we were certain that the properties of the components would be right on."
Before a final display of the animation, Fergen fine tuned the operating parameters of the simulation; assigning exact mass properties, velocity and force vectors with corresponding features in Working Model. "Suddenly we had an exact duplication of the problem we were examining," says Fergen. "Debugging the existing simulation was just a matter of observation on the screen and optimizing the motion profile through the timing chart from Excel."
The flexibility of the simulation environment also enabled Fergen to examine secondary variables that might not ordinarily merit consideration in a time-critical re-design. "We could experiment to see how a change in mass would help. In this particular instance, mass was a less important consideration; we might have ignored it entirely, but it’s so easy to plug in new values in Working Model and observe the changes that we were able to do it without devoting a lot of time to it."
Repairs in the Virtual World
With the faulty profile of the cam plainly illustrated, Fergen set about a sequence of corrections in the cam profile, all the while observing possible interferences that would affect functions elsewhere in the machine. Examining the new timing diagram and simulation he realized that the cam required only one dwell in the motion profile and that the boxy motion of the pick-and-place arm could be replaced by a semi-elliptical pattern to reduce jerk while avoiding interferences. "It made much more sense than a rigid motion full of right angles and stops, especially when you saw it functioning in Working Model." states Fergen.
Satisfied that the Working Model simulation revealed a far superior cam profile, Fergen imported the Working Model file back into AutoCAD to create a detailed drawing and prepare the file for transfer to CAM software. From there the new design was sent for fabrication on an in-house CNC machine.
Validation of the virtual prototyping process came immediately after installation of the new, improved cam, according to Fergen "We received the cam from the machine shop, installed it and had the machine working better than it ever had. Using the modifications that were created through the Working Model simulation, we were able to increase the machine speed by 20 percent while reducing vibration."
Large companies like Abbott Labs will likely continue to reap the benefits of virtual prototyping and simulation as product development teams, engineers, and maintenance personnel continue to save time and materials. But some benefits that giants like Abbott are realizing now may mean similar gains for smaller engineering firms. Because products like Working Model permit more complete examination of design alternatives, pre-existing or obsolete designs may find new life in re-engineered form. Abbott is currently applying this approach. "We'll be able to take off-the-shelf parts and optimize them for our needs. We anticipate that we'll be able to increase the speed of other machines by 35 percent by finding an optimum cam profile using Working Model."
Fergen is impressed with the design possibilities that are afforded by compatible software that can collect performance data, create objects with real world properties, and accurately simulate their functions. "If you were just generating data in Excel, for instance, you wouldn’t get very far in understanding a problem, just a lot of charts, but by simulating an event for which a spreadsheet or CAD software provide the parameters, you create a means of feedback. That kind of engineering information is invaluable."