Dynamic Designer Motion
Motion Simulation embedded in Inventor
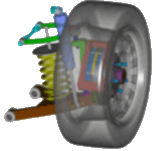
Motion/Professional Applications
Evaluate an unlimited number of design alternatives before you build and test a physical prototype.
Size motors and actuators
If you use motors, you have probably experiences problems like underestimating peak motor torques, failure to account for dynamic structural loading during machine operation, unable to predict the performance of non-linear systems and long/xpensive workout periods for prototype machinery. Dynamic Designer can solve these problems.
Determine power consumption
Determing actuator power consumption is immediately available in an XY plot. Power consumption is a quantity calculate from the motion simulation results.
Determine boundary conditions for stress analysis
If you are like most companies you use experience and guesses as boundary conditions for your FEA. Make FEA more than just a guess. Use the loads from Dynamic Designer to improve the accuracy of your FEA.
Friction
See how friction will increase power requirements and actuators size.
Force Transmission
Understand how forces are transmited through a mechanical system.
Spring and Damper Stiffness
You can see the effect of spring/damper systems on system motion, quickly experiment with spring/damper rates, and model non linear spring/damper effects.
Hydraulic actuators
Understand the forces required for hydraulic actuators.
Reduce vibrations
Identify vibration problems and reduce them using elements like motion dampers.
Understand unbalance effects on mechanisms
You will see how a unbalanced mass can effect the motion and how it transmits loads throughout the system.
Understand bearing loads
Make sure your mechanism does not exceed the loading conditions for your flat, ring, or ball bearings.