Dynamic Designer Motion
CAD Embedded Motion Simulation
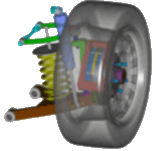
Can It Handle the Worst-Case Scenario?
Engineering consultants Unlimited, Inc. used Dynamic Designer/Motion simulation software, embedded in CAD, to study and validate the performance of a large glass-pressing machine under normal and maximum loading conditions. |
||
Oury’s team uses CAD software, then applies a complementary tool, Dynamic Designer Motion from Design Simulation Tehcnologies, Inc. (Canton, MI), to simulate and study design performance prior to committing to costly physical prototypes and testing. Dynamic Designer/Motion is embedded within the CAD system, so Oury and his team can deploy fully functional 3D dynamic simulation directly on their CAD assemblies. Oury particularly appreciates Dynamic Designer/Motion’s ability to simulate complex motion. Unlimited’s applications of the software include interference analysis, simulating loading during normal operation, crash testing, and analyzing forces resulting from part and assembly movement. "The technology allows us to quickly learn where analysis is needed without investing heavily in research and training," says Oury. "We obtain useful results very quickly, and that impresses our customers a great deal. It’s also an excellent tool for communicating simulation analysis results to non-engineering customers." |
||
"We obtain useful results very quickly. It’s an excellent tool for communicating results to non-engineering customers." |
||
Crashworthiness ProjectRecently, E-Tech Systems contracted Oury to help study the performance of a Lynch glass-pressing machine. Lynch is the premier manufacturer of press machines and industrial controls for the world’s consumer and electronic glass industries, including high-definition television picture tubes. Unlimited’s challenge with the Lynch design was to determine torque caused by a damping cyclinder failure under normal operating and crash conditions, as well as the vertical force caused by both normal operation and a crash. With just a two-week window to run the analysis and an additional week to deliver results, Oury and his team first modeled the machine using the CAD system, then used Dynamic Designer/ Motion for all dynamic simulations. The machine’s adjustable base was fixed in space on the axis of table rotation and forces, and moments were taken. Assemblies were created for each moving body, and parts were reorganized so they were in appropriate assemblies for motion analysis. The ram and plunger densities were adjusted to meet the specified weights of 1,600 pounds for the mold and 1,320 lbs. for the plunger. Total weight of the system is approximately 175,000 pounds. Having set these parameters, Oury defined the normal operation for table rotation at specific speeds. Then, damping was removed, and a crash was allowed to occur. The process was driven by a constant-drive ram force to simulate the hydraulic cylinder, and damped by constant-cushion drive forces sufficient to rotate the table in the specified time. Time and Cost SavingsBy simulating the crash test, Oury was able to determine optimum normal-operation and worst-case mounting pad loading factors so civil engineers could design the concrete base for the glass-pressing machine. |
||
"I simply refined the model in CAD, and the changes were reflected in the motion model." |
||
"Traditionally, to obtain these types of variables, companies spend a lot of time and money building and crashing physical equipment," Oury says. "Without simulation, we would have had to rely on complex manual calculations and set-ups. Using Dynamic Designer/Motion helps eliminate these steps and speeds time to market. Lynch was so impressed with our results from the product, they recently purchased the software themselves." On the last day of the project, Lynch requested a considerable amount of additional information related to the work Oury had just completed. "I was able to easily accommodate this as a result of using Dynamic Designer/ Motion. I simply refined the model in CAD, and the changes were reflected in the motion model. This seamless integration makes Dynamic Designer/ Motion an invaluable tool for meeting design challenges." |