Working Model 2D
2D Dynamic Motion Simulation
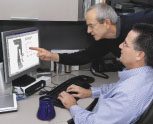
Industrial Equipment Manufacturer Optimizes New Equipment Design with Working Model
In designing this industrial smelt spout cleaner, Clayton Abel, a product engineer for Anthony-Ross, used Working Model to determine dynamic loads for parts moving along a complicated path.
From concept to completion, designers of automated industrial equipment face a significant challenge when they implement proposed features into a new product design. How does an engineer know with complete certainty that he is producing the optimum design for a product that must withstand rigourous operating requirements? Clayton Abel, a product development engineer with Oregon-based Anthony-Ross Company, an industrial engineering firm that designs paper mill equipment, recently found the solution to this challenge. When Abel was given the project of designing a complex piece of machinery, he realized that the key to achieving flawless automation would be found in the repeated testing of the model in the early stages of the design.
Unfortunately for most engineers, the extensive testing of anticipated stresses upon their designs means either developing costly prototypes, or spending valuable time developing an endless series of geometric equations. Abel knew that he could bypass both of these obstacles by using Working Model 2D, desktop motion analysis software made by Design Simulation Technologies. Abel saw an ad for Working Model and sent away for information. At the time, he was using a similar product, so he was familiar with desktop motion analysis software. But once he purchased Working Model and realized its capabilities, Abel never used the old software again.
"It was a good program, but not as convenient as Working Model," said Abel, who used Working Model to help him customize designs for Anthony-Ross trademark product. For more than ten years, Anthony-Ross has manufactured Automated Port Cleaners (APCs), devices that clean ports in recovery furnaces used in the pulp and paper industry. Recovery furnaces are the chemical recycling centers of pulp and paper mills.
It takes large quantities of expensive chemicals to break down wood chips into pulp. The pulp created from this procedure goes in one direction to be made into paper, while the spent chemicals and leftover organic matter are sent to a recovery furnace to be burned. These boilers are ninety-nine percent effective in recovering chemicals for recycling, so there is little pollution or waste involved in the process.
Smelt Spout Cleaner.
The heat from the furnace reduces the chemicals, which fall to the bottom of the burner and melt into a black liquid called smelt. Recently, Anthony-Ross decided to expand its line of automated equipment with a smelt spout cleaner, an apparatus for cleaning spouts that drain smelt from the bottom of the furnaces. If smelt is not drained regularly and thoroughly, it freezes and forms a crust that clogs the smelt spout, which causes the level of smelt inside the furnace to rise. This decreases the amount of chemicals that can be recovered and increases the amount of noxious chemicals released. Before the smelt spout cleaner was introduced, the only effective method of spout cleaning involved workers inserting long rods into the spout to dislodge char and encrusted material. This is a physically demanding job that exposes workers to potentially hazardous fumes and the danger of being splashed by the molten smelt.
Abel faced several challenges in the creation of the new smelt spout cleaner. The product had to sit well away from the furnace so it wouldnt be exposed to corrosive fumes and so that it could be repaired or relocated quickly without disturbing the burning furnace. The cleaner had to be able to sense any misalignment between itself and the spout, as well as any thermal expansion taking place within the spout, so it could follow spout movement. In addition, since different boilers have different spout designs, Abel wanted to create a cleaner that would not have to be customized for each installation.
The proposed design involved a long horizontal beam attached to a camming track. The beam would move back and forth over the spout and rake loose the frozen smelt. Then paddles attached to the beam assembly would unfold, lock into place, and scrape out the loosened materials. DXF IMPORT. Abel created the design in AutoCAD, then separated it into sections and exported them in DXF files to Working Model. He then assigned properties such as mass, density and coefficients of friction to the different components to control how they interacted with each other.
Before he could begin testing the parts, Abel linked them together. "Working Model provides all the built-in actuators, motors, springs, dampers and pin joints needed to construct realistic models," he said. "With my old software, I had to write equations for all those devices and create them from scratch within the program. With Working Model, just click on an icon to select a device, and place it on the object by dragging it there with the mouse."
Once the parts were joined, Abel imposed anticipated working loads upon various components of the smelt spout cleaner. "My goal was to reduce the stress on machine elements as much as possible," he said. "Too much stress will cause parts to wear out quickly."
One of the most challenging aspects of the smelt spout cleaner design was the moving beam assembly supported by cam rollers in a track. The track had an almost roller-coaster shaped design. It had to be precisely shaped so the beam could move freely without coming in contact with the spout. Not only did the track have to support the weight of the beam, but it had to allow for extensive cam roller movement as the beam moved in a simultaneous up-and-down, in-and-out fashion.
"It would be difficult to manually calculate the loads on the track," said Abel, "but Working Model did it automatically. It allowed me to look at eight or ten different track configurations in a day, and I came up with the ideal shape. Without Working Model, it would have taken me a week or more to calculate that many geometries."
Another load Abel considered was the external force of the frozen smelt upon the beam and the cleaning paddles. "I modeled the smelt, added it to the simulation and looked at how it affected beam movement," said Abel. "This test made it obvious what size cam roller to choose." Abel used Working Models built-in actuators to model air cylinders. "I positioned the actuator at the base of the beam and ran a simulation," said Abel, "I was able to measure the forces required to reverse the direction of the beam as it raised and lowered above the spout. This allowed me to properly size the air cylinder for the job."
Quick & Accurate.
All these tests were accomplished quickly in Working Model. "Its easy to determine what the loads are for static tracks and rollers," said Abel. "Working Model is unique because it allows me to determine what the dynamic loads are as parts move along a complicated path." As Abels simulations ran, he watched graphs of the changing forces on the screen as well as compiled the recorded data in a tabular form, which he then printed for closer examination. Once Abel located the maximum forces, he entered the information into a finite-element analysis program. The results allowed Abel to substantially reduce the size and weight of the proposed product design.
"Working Model saved Anthony-Ross a significant amount of time in the development process," said Abel. "In addition, it gave us the assurance that the product we finally chose to produce is the best that we can do. If I had to manually do what Working Model did, I could not have looked at nearly as many configurations and might not have come across the best combination of geometries. Working Model is easy to use and very useful."
Abel is now in the process of designing another new product for Anthony-Ross. "The next project on the board is a port-damper assembly, which will control the air flow entering the recovery furnace," said Abel. "The product will have several links, pivots, spring tensioners and air cylinders, so its a natural design to analyze with Working Model."