Working Model 2D
2D Dynamic Motion Simulation
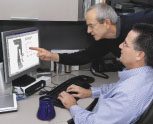
Articulated Boom Design Gets a Lift with Working Model
Snorkel Economy used Working Model to test its new design for side tip stability by varying both the boom load and the platform counter-weight. The analysis helped the designers ensure that industrial safety standards were met -- before the mobile lifter was physically prototyped.
Snorkel Economy of St. Joseph, Missouri is an OEM of self-propelled aerial work platforms that lift workers and their tools high in the air to perform tasks.
Snorkel Economy's mobile lifters are popular with construction companies, aerospace manufacturers, and other companies that need to place workers in hard to reach places. Snorkel Economy boom-type machine is stabilized solely on its tires; it does not have outriggers, special extensions or braces. Balance, therefore, is one of the most important specifications for the design engineers to consider early on in the design cycle.
27 Pin Boom Design
Recently, engineer Dave Engvall analyzed an articulated boom with 27 junctions known as pin joints where the sections of the boom connect and move, including a telescopic extension with a basket on the end that serves as the work platform. The boom had three main lift cylinders and two other cylinders for levelling the basket. Two aspects of Engvall's design were crucial: the stability of the entire vehicle, and the load on each one of the 27 pin joints.
"Our machines have to be stable in any position of articulation," explained Engvall, "so I needed to estimate the weight of each component, and then place the lifting structure in several different positions and determine how much counterweight would be necessary to maintain stability."
To test the feasibility of the design, Engvall imported his CAD files using DXF translators into Working Model®, a dynamics/kinematics analysis software package by Design Simulation Technologies. Working Model applies the laws of physics to mechanical designs and simulates the motions of objects. Working Model lets engineers see the physical consequences of their designs in graphic, animated form. Engvall could assign specific values to his design, such as the probable weight of each component, the forces acting on the basket at different extensions, and explore hypothetical situations such as placing the vehicle on an incline. As a result, Engvall could quickly abandon unrealistic models and narrow his design to one that would work in the real world.
Testing for Instability
Engvall's first task was to find the most unstable aspect of the new design. He focused his attention on the lifting structure -- consisting of the boom, the engine that drives it, and the counterweight that balances it -- all set on a turntable that rotates about a vertical axis in the middle of the vehicle chassis.
"I placed my model in a known critical stability orientation, and then I added weight to the counterweight until I made the situation stable," said Engvall. "It's not unlike those scales used in a doctor's office, where the idea is to balance the little metal weights until they are level." The hardest balancing problem for Engvall's design was side tip stability, with the boom extended at a right angle to the vehicle. The key point of balance or "tipping fulcrum" in this position was the tire.
"I modeled that situation with the tire on one side of the machine, and then I used an element in Working Model called a separator on the opposite side, which constrains two objects from getting closer together. They can get further apart, but not closer." The separator kept the tire (and, because they were joined by a fixed point, the entire vehicle) from intersecting the ground in order to keep the model balanced. Engvall then ran the simulation.
In just a few seconds, Working Model demonstrated at what point the mobile lifter was stable. When the force on the separator was less than zero, the machine tipped over. When it was greater than zero, it didn't.
"It's visually interesting to watch," Engvall noted, but the real satisfaction was in knowing that the mathematical data behind the simulation was highly accurate. "I have great confidence in the results," confirmed Engvall. "And it's much more enjoyable to watch the machine tip over in my mechanism model than in the real world. Using Working Model has greatly streamlined the calculations necessary to match the boom structure weight with the counterweight." Working Model's solved these calculations to an 80-bit number with a floating point that allowed the calculations to be performed faster with greater accuracy.
Getting the weight just right means Snorkel Economy will be able to manufacture a machine that not only meets ANSI safety standards, but optimizes the best type and weight of materials to use to keep production costs from becoming prohibitive.
"If you put more cost into a part, you can save weight," explained Engvall, "but there are a lot of tradeoffs to consider such as how expensive a material you want to use to save weight." In Working Model, the weight of each component can be controlled, and if too much counterweight was needed to make Engvall's design stable, then he had to reduce the weight of some of the other components.
Engvall tested the stability of all the pin joints, running his simulations over and over to refine the ratio between material weight and the optimum articulation of all the boom joints and struts.
Meeting European Safety Standards
Achieving side tip stability didn't mean Engvall could proceed with his design. He had to check his boom/counterweight balance combination in other articulations, too. Snorkel Economy must test for back tip stability (with the boom fully extended overhead), and for external forces which could act upon the basket, such as wind. Working Model's Smart Editor feature allowed Engvall to reposition his mobile lifter intact in any configuration, quickly modify any physical forces with its easy-to-use graphical user interface, then run a new simulation in a matter of seconds. Engvall could play back the simulations frame-by-frame, in real time, or in a quicker mode. Engvall even simulated different force and balance specifications to meet European safety requirements. Designing a mobile lifter that requires fewer part substitutions to meet another country's safety standards means Snorkel Economy will save money making fewer modifications to its vehicles for sales to foreign customers.
Measuring Forces for FEA Analysis
Measuring the load stress or static force balance on individual pin joints was the other major application that Working Model helped Engvall simulate. The weight of a pin affects the load on all the pins, so if unacceptably high stress is found to effect one pin, then that junction will require a bigger pin, which in turn increases the loads on the other pins.
"This is the simplest application of a mechanism model, but it is extremely useful for me," said Engvall. "If I did the static force balance analysis myself, I would have to describe a free body diagram of each component, write equations for the translations and rotational elements for each link, and solve them all simultaneously. It's very time consuming."
Instead, Engvall used Working Model to assign the proper weight to each component, and then put a pin joint at each location so the components could move and then let the simulation run. This determined the pin loads on all the joints. In this way, Engvall was able to accurately measure the forces for finite element analysis.
"The model doesn't have any idea how much a pin can hold, so it just loads it up with whatever it takes to achieve equilibrium," explained Engvall. After measuring the static load on each of the pins, Working Model provided the results that Engvall shared with a stress analysis engineer, who then examined the design of the connecting brackets in the boom using finite element analysis to make sure they could accept those loads.
Confidence in the Results
Using Working Model has saved Engvall countless manhours. It used to take more than a week to create his models and do his static load calculations, but now he can do both in a single morning, and the simulations themselves take a matter of seconds to complete. "What I like about Working Model is that I have confidence in the results," said Engvall. "When I run simultaneous simulations, the result is graphically clear and reliable."
Using dynamic/kinematic analysis, Snorkel Economy has leapfrogged one time-consuming portion of its design analysis cycle before prototyping a single part. The ability to test the feasibility of his articulated boom design in Working Model means Engvall helps his company get its products to market faster using the most cost effective amount of raw materials.
"For what it costs and what it does, Working Model is an astounding piece of software," Engvall concluded.
Snorkel Economy
Snorkel Economy is a 500+ employee company located in St. Joseph, MO. They are one of the leaders in the industrial mobile access market (aerial work platforms). Snorkel Economys customers include large construction companies, rental yards, and aerospace corporations.