Working Model 2D
2D Dynamic Motion Simulation
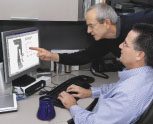
Prototyping High Volume Production Equipment at Gillette
The above image shows Gillettes ball point pen hopper design operating at an agitator frequency of 7 rad/sec. Gillette went immediately from a Working Model simulation to building production line equipment, completely avoiding physical prototyping. Note that Working Model is automatically handling thousands of pen collisions at each integration step.
Mechanical engineers at Gillette Corporation in Santa Monica, California have turned to motion simulation and virtual prototyping to help reduce production line down time and keep their disposable ball-point pen manufacturing line in operation. With a dynamics/kinematics software package called Working Model, engineers are designing, testing, prototyping and troubleshooting manufacturing equipment more efficiently.
Jose Ortiz, a manufacturing engineer at Gillette, has used Working Model with success on several projects over the past few months. According to Ortiz, "Working Model is an extremely powerful tool on the manufacturing floor."
Pen Refill Hopper
Working Model has proved itself particularly invaluable during the design of a pen refill hopper used to funnel thousands of pens into two chutes. A previous hopper was prone to jamming When a jam occurred, pen production ground to a halt. Engineers at Gillette proposed that a new hopper with strategically placed agitators be designed to replace the faulty piece of machinery.
In the past, engineers at Gillette would have done the entire hopper design in a CAD package. A physical prototype would then be built and tested. Prototypes commonly needed several modifications before the machinery was fully operational. This process was both expensive and time consuming.
The Virtual Prototype
With Working Model, Ortiz was able to create a simulation of a fully functioning virtual prototype. This model enabled Gillette to analyze the hopper design in a fraction of the time it would have taken to machine a physical prototype. Ortiz tested several different agitator configurations and speeds. Geometries were quickly varied by simple click and drag mouse commands, and agitator speeds were interactively changed between runs using a Working Model input control. The optimal hopper design Ortiz arrived at is shown in operation in the figures above.
Avoiding Physical Prototyping
Confident of his design due to the testing done with Working Model, Ortiz immediately built the production model of the hopper, completely avoiding physical prototyping. The pen refill hopper operated exactly as it was simulated in Working Model. No design modifications were needed, and Ortiz says that the new hopper has yet to jam since being installed in the production line.
Ortiz estimates that Working Model saved them several weeks, if not longer, on this project. And, he states, "It continues to save us time and money as we troubleshoot production problems."
The Analysis Tool
Working Model is a kinematics/dynamics software package that allows users to model and analyze almost any mechanical device. With Working Model, engineers can improve the design of anything that moves -- from simple mechanisms to highly complex machinery. It is being used by thousands of companies at all stages of the product life cycle. In manufacturing, Working Model is being used to design bottling machinery, printing presses, bagging equipment, stamping equipment, and much more.
Working Model is unique in that it is both accurate and easy to use. Creating simulations with Working Model takes only a fraction of the time needed for traditional Unix based dynamics/kinematics packages. Users can import DXF geometries from a CAD package, or draw and create simulations in Working Model from scratch. No equation writing is needed -- Working Model handles all motion computations, including collisions, automatically. Yet even with its ease-of-use, Working Model provides highly accurate results. With 80 bit numerics, Working Model provides more precision than typical CAD packages.